3D printing is reshaping rocket development by revolutionizing manufacturing processes. You can now create rocket components faster and at a fraction of the cost compared to traditional methods. For instance, Blue Origin leveraged 3D printing to replace parts that took over a year to produce with components ready in just months. Similarly, 82% of manufacturers report significant cost savings by adopting this technology.
In space exploration, 3D printing is advancing satellite launches by enabling lightweight and complex designs. Compact communication satellites benefit from customized components like antennas and housings, improving performance while reducing weight. Industry leaders like SpaceX and Blue Origin demonstrate how this technology accelerates production and enhances scalability, paving the way for more efficient rockets and spacecraft.
Key Takeaways
- 3D printing speeds up rocket building by saving time and money.
- It helps make light and complex rocket parts, improving fuel use.
- Companies like SpaceX and Relativity Space use it for cheaper rockets.
- New 3D printing tech will change how space tools are made.
- Learning about 3D printing can help find new space ideas.
The Role of 3D Printing in Aerospace
Additive manufacturing and its impact on aerospace innovation
Additive manufacturing is reshaping the aerospace industry by enabling faster production cycles and reducing costs. This transformative approach allows you to create intricate designs that were previously impossible with traditional methods. The aerospace and defense additive manufacturing market, valued at $4.46 billion in 2023, is projected to grow to $18.56 billion by 2030. With a compound annual growth rate of 18.8%, this technology is driving innovation across the aerospace sector.
By leveraging 3D printing technology, you can produce lightweight components that enhance fuel efficiency and reduce payload weight. This capability is critical for rockets and spacecraft, where every gram matters. The aerospace industry benefits from the ability to iterate designs rapidly, ensuring optimal performance and reliability.
Why 3D printing is essential for modern rocket development
3D printing technology is revolutionizing rocket development by offering unparalleled advantages in cost and time efficiency. For example, iterative design processes that once required months can now be completed in weeks. You can achieve up to five design iterations before traditional methods complete just one.
Evidence Description |
Cost Reduction |
Time Reduction |
---|---|---|
Iteration of designs |
Less than one iteration |
Five iterations possible |
Engine production |
40% of total rocket cost |
90% turnaround time reduction |
Combustion chamber production |
Significant reduction |
Manufactured within weeks |
Injector head redesign |
50% cost reduction |
Lead times three times lower |
These metrics highlight how 3D printing technology accelerates rocket development while minimizing expenses. By adopting additive manufacturing, you can streamline production processes and focus on innovation rather than logistical challenges.
Key milestones in the adoption of 3D printing for rockets
The aerospace industry has achieved remarkable milestones in integrating 3D printing into rocket development. Firehawk Aerospace demonstrated significant progress by successfully testing rocket engines and 3D-printed fuel. This achievement underscores the growing reliability of additive manufacturing in critical applications.
Industry leaders like SpaceX and Relativity Space continue to push boundaries by incorporating 3D printing technology into their rockets. These advancements pave the way for fully 3D-printed spacecraft, reducing costs and increasing accessibility for space exploration. As you explore the potential of additive manufacturing, you’ll find that its impact extends far beyond production—it’s shaping the future of aerospace innovation.
3D Printing Technologies in Rocket Development
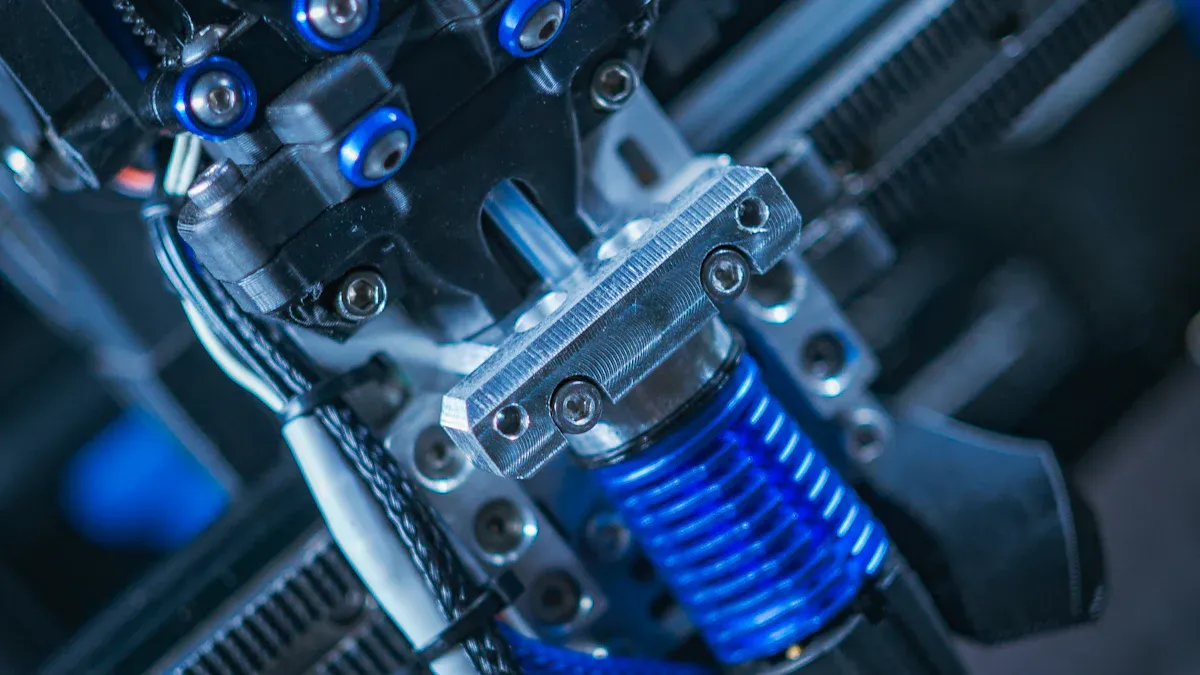
Selective Laser Melting (SLM) for precision components
Selective Laser Melting (SLM) stands out as one of the most advanced metal 3D printing technologies for rocket development. This process uses high-powered lasers to fuse metal powders layer by layer, creating intricate and durable components. You can achieve exceptional precision with SLM, making it ideal for manufacturing critical rocket parts like combustion chambers and injector heads.
SLM enables the production of lightweight structures with complex geometries that traditional machining cannot replicate. NASA has demonstrated the effectiveness of SLM by producing a flying model rocket with complex engine components, significantly reducing production time. Relativity Space has also leveraged SLM to streamline production and enable rapid prototyping for entire rocket structures.
Organization |
Case Study Description |
Performance Metrics |
---|---|---|
NASA |
3D printed flying model rocket with complex engine components |
Reduced production time significantly |
Relativity Space |
Entire rocket structures produced using additive manufacturing |
Streamlined production and rapid prototyping |
Various Startups |
Cost savings achieved through advanced 3D printing techniques |
Enhanced performance capabilities and reduced operational expenses |
By adopting SLM, you can optimize rocket designs for performance and reliability while minimizing production costs and lead times.
Direct Energy Deposition (DED) for large-scale manufacturing
Direct Energy Deposition (DED) is a powerful metal 3D printing technology designed for large-scale rocket manufacturing. This process involves depositing metal powders or wires directly onto a substrate using a focused energy source, such as a laser or electron beam. DED excels in producing dense and strong parts with mechanical properties comparable to cast or wrought materials.
You can use DED to create near-net-shape components, reducing the need for extensive post-processing. It is particularly effective for manufacturing larger rocket parts, such as fuel tanks and structural supports. Sciaky’s EBAM printers, for example, can produce parts several meters high, showcasing the scalability of DED for aerospace applications.
Metric |
Description |
---|---|
High build rates |
DED offers faster build rates compared to other metal additive manufacturing processes. |
Dense and strong parts |
Parts produced are of higher density with mechanical properties comparable to cast or wrought materials. |
Near net shape |
Parts can be produced close to their final shape, minimizing the need for post-processing. |
Repair capabilities |
DED is suitable for adding material to existing parts, making it ideal for repairs. |
Multi-material range |
New DED machines can utilize various powders or wires, allowing for custom alloy construction. |
Larger parts |
DED can manufacture larger components, with examples like Sciaky’s EBAM printers capable of printing parts several meters high. |
Easy material change |
The process allows for on-demand material feeding, facilitating easy changes during production. |
Reduced material waste |
DED minimizes waste by depositing only the necessary material, unlike other methods that require filling the entire build platform. |
DED also offers repair capabilities, allowing you to add material to existing parts, which is invaluable for maintaining and upgrading rocket systems. Its ability to minimize material waste further enhances cost efficiency, making it a preferred choice for large-scale manufacturing in aerospace.
Emerging 3D printing technologies in aerospace
The aerospace industry continues to embrace emerging 3D printing technologies to meet the growing demand for lightweight, customizable, and high-performance rocket components. Innovations in materials and additive manufacturing techniques are driving this evolution.
- The global 3D printing materials market is projected to grow at a CAGR of over 20% through 2027.
- The aerospace 3D printing market is expected to reach $3.5 billion by 2024.
- Adoption of 3D printing in aerospace is fueled by the need for lightweight components, customization, and rapid prototyping.
These trends highlight the increasing reliance on 3D printing technologies for rocket development. You can expect breakthroughs in multi-material printing, advanced alloys, and hybrid manufacturing systems that combine additive and subtractive processes. As these technologies mature, they will further reduce costs and expand the possibilities for rocket design and production.
Benefits of 3D Printing for Rockets
Rapid prototyping for accelerated development cycles
3D printing has revolutionized prototyping in rocket development by enabling faster iterations and shorter timelines. Traditional manufacturing methods often require weeks or months to produce prototype parts. In contrast, 3D printing allows you to create functional prototype parts in days, significantly accelerating the development process.
- Rapid prototyping through 3D printing fosters innovation by allowing you to test and refine designs quickly.
- The technology reduces the time between design iterations, enabling faster testing phases and shorter development cycles.
This capability is particularly valuable in the aerospace sector, where delays can lead to substantial cost overruns. By leveraging 3D printing technology, you can streamline the prototyping process and focus on optimizing rocket performance.
Cost efficiency through material savings and streamlined production
3D printing technology offers unparalleled cost efficiency in rocket development by minimizing material waste and simplifying production processes. Unlike traditional methods, which often involve machining away excess material, metal 3D printing uses only the necessary amount to create each part. This approach reduces waste and lowers material costs.
Evidence Type |
Description |
---|---|
Cost Reduction |
Significant cost reduction associated with 3D printing technologies compared to traditional methods. |
Material Waste Reduction |
Substantial reduction in material waste by using only necessary material for part creation. |
Rapid Prototyping and Testing |
Ability to quickly produce and iterate on designs, leading to faster innovation and development. |
Design Flexibility and Customization |
Greater design flexibility allows for optimized performance tailored to specific mission requirements. |
For example, 3D printing can reduce sand casting costs by up to 75%. Conventional production methods might cost around €3,600, while 3D printing reduces this to approximately €900. Additionally, the elimination of core assembly shortens the production timeline, further enhancing cost efficiency.
Design flexibility for complex geometries and lightweight structures
One of the most significant advantages of 3D printing is its ability to produce complex geometries and lightweight structures that traditional manufacturing cannot achieve. This design flexibility allows you to optimize rocket components for performance and reliability.
- 3D printing enables the creation of intricate combustion chambers as a single piece, reducing potential failure points.
- The technology facilitates the integration of multiple components into a single structure, simplifying assembly and enhancing durability.
- Lightweight structures can be achieved through advanced materials and optimized internal geometries, leading to significant weight savings.
"AM provides a revolutionary and transformative way to manufacture products on earth and it’s the same for in-space applications. It allows us to do things in space in ways we’ve never done before." - John Vickers, NASA
SpaceX has demonstrated the practical applications of 3D printing by using it to manufacture parts for its Merlin and Raptor engines. These innovations highlight how 3D printing technology enhances design flexibility, enabling you to create rocket components tailored to specific mission requirements.
Improved performance and reliability of rocket systems
3D printing has significantly enhanced the performance and reliability of rocket systems, making it a cornerstone of modern aerospace development. By enabling precise manufacturing processes, this technology ensures that critical components meet the highest quality standards. You can now achieve levels of accuracy and consistency that were previously unattainable with traditional methods.
One of the key ways 3D printing improves performance is through the integration of advanced quality control techniques. For example:
- Industrial CT scanning allows you to inspect 3D-printed rocket components for internal flaws, ensuring their structural integrity.
- Adjustments in the printing process, based on detected flaws in cooling channels, have led to higher-quality parts and reduced material waste.
- Early detection of incomplete fusions in combustion chambers has prevented potential engine failures, optimizing future production runs.
These advancements not only enhance the reliability of individual components but also contribute to the overall safety and efficiency of rocket systems.
The ability to produce complex geometries with metal 3D printing plays a crucial role in improving rocket performance. You can design intricate cooling channels within combustion chambers, which optimize heat dissipation and improve engine efficiency. This level of customization ensures that each component performs at its best under extreme conditions.
Moreover, 3D printing reduces the number of parts required in a rocket by consolidating multiple components into a single structure. This simplification minimizes potential failure points, leading to more reliable systems. For instance, SpaceX has utilized 3D printing to manufacture parts for its engines, resulting in fewer assembly steps and enhanced durability.
The iterative nature of 3D printing also contributes to better performance. You can quickly test and refine designs, ensuring that each iteration meets stringent aerospace standards. This rapid feedback loop accelerates development cycles and allows you to focus on optimizing performance rather than troubleshooting manufacturing issues.
Real-World Applications of 3D-Printed Rockets
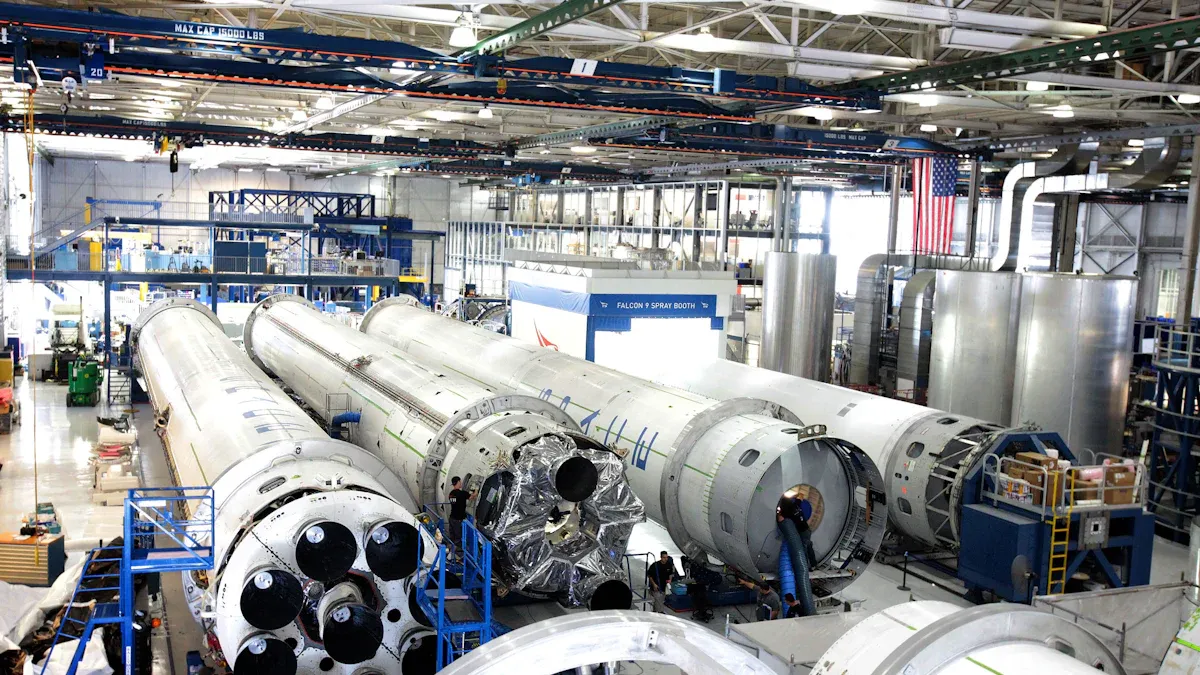
Rocket Lab’s Rutherford engine and its 3D-printed components
Rocket Lab’s Rutherford engine exemplifies the transformative potential of 3D-printed rockets. This engine incorporates 3D printing for 95% of its components, including the combustion chamber, injector, and turbopumps. By leveraging additive manufacturing, Rocket Lab has achieved remarkable efficiency in production. Critical parts are manufactured within 24 hours, significantly reducing lead times compared to traditional methods.
The Rutherford engine also demonstrates cost-effectiveness. Each launch costs approximately $7.5 million, making it one of the most affordable options in the aerospace industry. With a success rate of 95% across more than 40 launches, the engine has proven its reliability. In 2023, Rocket Lab further showcased its innovation by reusing the Rutherford engine, highlighting the sustainability of 3D-printed rocket components.
Metric |
Value |
---|---|
3D-Printed Components |
|
Launch Cost |
$7.5 million |
Production Speed |
Parts produced in 24 hours |
Success Rate |
95% over 40+ launches |
Reusability |
Engine reused in 2023 |
SpaceX’s use of 3D printing in SuperDraco thrusters
SpaceX has integrated 3D printing into its SuperDraco thrusters, which are critical for the Dragon spacecraft’s launch escape system. These thrusters are manufactured using a process called direct metal laser sintering (DMLS), enabling the creation of intricate geometries that enhance performance.
The use of 3D printing has allowed SpaceX to produce SuperDraco thrusters with fewer parts, reducing potential failure points and improving reliability. This innovation has been instrumental in ensuring the safety of crewed missions, as the thrusters provide rapid and precise thrust during emergencies. SpaceX’s adoption of 3D printing underscores its commitment to advancing rocket technology through cutting-edge manufacturing techniques.
Relativity Space’s Terran 1: A fully 3D-printed rocket
Relativity Space has taken 3D printing to new heights with its Terran 1, the world’s first fully 3D-printed rocket. Approximately 95% of the rocket is produced using additive manufacturing, including its structure and engines. This approach has significantly reduced lead times and production costs, enabling faster development cycles.
Relativity Space has raised $500 million in funding to support its innovative approach. The company’s use of 3D printing has resulted in substantial cost savings and streamlined production processes. By reducing the number of parts required, the Terran 1 minimizes assembly complexity and enhances reliability. This groundbreaking achievement highlights the potential of 3D-printed rockets to revolutionize the aerospace industry.
Metric |
Value |
---|---|
Percentage of rocket produced |
95% |
Total funding raised |
$500 million |
Reduction in lead times |
Significant |
Cost savings from 3D printing |
Substantial |
Note: Companies like Boom Supersonic, TRUMPF, and UTC Aerospace are also leveraging 3D printing for aerospace applications. The global aerospace 3D printing market, valued at $3.13 billion in 2023, is projected to grow at a CAGR of 20.6% through 2030. This growth reflects the increasing demand for customization and rapid prototyping in rocket development.
NASA’s advancements in 3D-printed rocket technology
NASA has been at the forefront of innovation in 3D-printed rockets, leveraging cutting-edge technologies to redefine how rocket components are designed and manufactured. By adopting advanced additive manufacturing methods like laser powder bed fusion and directed energy deposition, NASA has achieved remarkable breakthroughs in producing high-strength parts comparable to forged metals. These methods allow you to create intricate designs that enhance performance while reducing weight and costs.
One of NASA’s most notable contributions is the development of GRCop alloys, specifically engineered for rocket engines. GRCop-84, for instance, can endure temperatures up to 6,000 degrees Fahrenheit and has been tested to last 100 missions between maintenance cycles. This durability significantly outperforms traditional materials. The latest GRCop-42 alloy takes this innovation further by enabling the production of single-piece combustion chambers. This advancement not only improves engine efficiency but also simplifies manufacturing processes.
NASA’s research has also paved the way for creating fully 3D-printed rockets. The Terran 1 rocket, standing 100 feet tall and 7.5 feet wide, was the first test rocket made entirely from 3D-printed parts. This milestone demonstrates how additive manufacturing can streamline production and reduce lead times. By integrating these technologies, you can achieve faster development cycles and more reliable rocket systems.
These advancements highlight NASA’s commitment to pushing the boundaries of aerospace engineering. By utilizing 3D printing, you can optimize rocket designs for performance, durability, and cost-efficiency, setting new standards for the industry.
The Future of 3D Printing in Rocket Development
The potential for fully 3D-printed rockets and spacecraft
The future of aerospace lies in the potential for fully 3D-printed rockets and spacecraft. Companies like Relativity Space are leading this transformation by developing the Terran 1 and Terran R, which are nearly entirely 3D-printed. These rockets can be manufactured in just 60 days, a fraction of the time required by traditional methods. NASA has also embraced this innovation, using 3D printing to create complex rocket engine components. Fleet Space is taking this technology further by planning a constellation of fully 3D-printed satellites.
Company |
Contribution |
Timeframe to Flight |
---|---|---|
Relativity Space |
Developing Terran 1 and Terran R, the first fully 3D-printed rockets. |
~60 days |
NASA |
Creating rocket engine parts using 3D printing for complex components. |
N/A |
Fleet Space |
Planning to launch a constellation of fully 3D-printed satellites. |
N/A |
This shift toward 3D-printed spacecraft manufacturing reduces production timelines and enhances scalability. By adopting this approach, you can expect faster innovation cycles and more accessible space exploration opportunities.
Innovations in materials and additive manufacturing techniques
Advancements in materials and additive manufacturing techniques are driving the next generation of space travel. New titanium alloys, created through AI-enhanced 3D printing, are 66% lighter than traditional materials. These alloys improve fuel efficiency and reduce costs for satellite launches. Additionally, on-demand production minimizes inventory requirements and material waste, aligning with sustainability goals.
You can also leverage 3D printing to produce radiation-shielding polymers and heat-resistant alloys for spacecraft. These materials enhance the durability of spacecraft components, making them suitable for long-term missions. As these innovations mature, they will redefine spacecraft manufacturing by enabling the creation of lightweight, high-performance designs tailored to specific mission requirements.
Evidence Type |
Details |
---|---|
Cost Reduction |
AI has enabled the creation of titanium alloys that are 66% lighter than traditional materials, reducing costs for satellite launches and improving fuel efficiency in aircraft. |
Sustainability |
On-demand production reduces inventory requirements and material waste, contributing to sustainability goals. |
Space Exploration Applications |
AI-enhanced 3D printing is used to produce radiation-shielding polymers and heat-resistant alloys for spacecraft, improving accessibility for long-term missions. |
Reducing costs and increasing accessibility for space exploration
3D printing is revolutionizing rocket development by significantly reducing costs and increasing accessibility for space exploration. Traditional tooling, often expensive and time-consuming, is no longer necessary. This technology minimizes material waste, further lowering production expenses. Studies suggest that 3D printing can reduce the cost of producing rocket parts by 30-40%, making space missions more economically viable.
- 3D printing eliminates the need for traditional tooling, reducing costs.
- It minimizes material waste, leading to further cost savings.
- The production of rocket components is faster, enhancing efficiency.
- Studies indicate that 3D printing could lower the cost of producing rocket parts by 30-40%, making space missions more economically viable.
By adopting 3D printing, you can streamline spacecraft manufacturing processes and focus on innovation. This approach not only reduces costs but also democratizes access to space, enabling smaller organizations to participate in the next generation of space travel.
Ongoing research and the future of aerospace manufacturing
Ongoing research in 3D printing is transforming aerospace manufacturing, paving the way for groundbreaking advancements. Scientists and engineers are exploring innovative techniques to enhance efficiency, reduce costs, and improve the performance of rockets and spacecraft. These efforts are shaping the future of aerospace technology.
One area of focus is the development of Selective Laser Sintering (SLS) for manufacturing aerospace components. SLS offers remarkable improvements over traditional methods, as shown in the table below:
Metric |
Traditional Manufacturing |
SLS Manufacturing |
Improvement |
---|---|---|---|
Weight Reduction |
Baseline |
70% |
|
Cost Savings |
Baseline |
Up to 90% |
90% |
Lead Time |
Baseline |
Reduced by 50-80% |
50-80% |
Part Consolidation |
Baseline |
Up to 100 parts into 1 |
99% |
Fuel Efficiency |
Baseline |
Up to 25% |
25% |
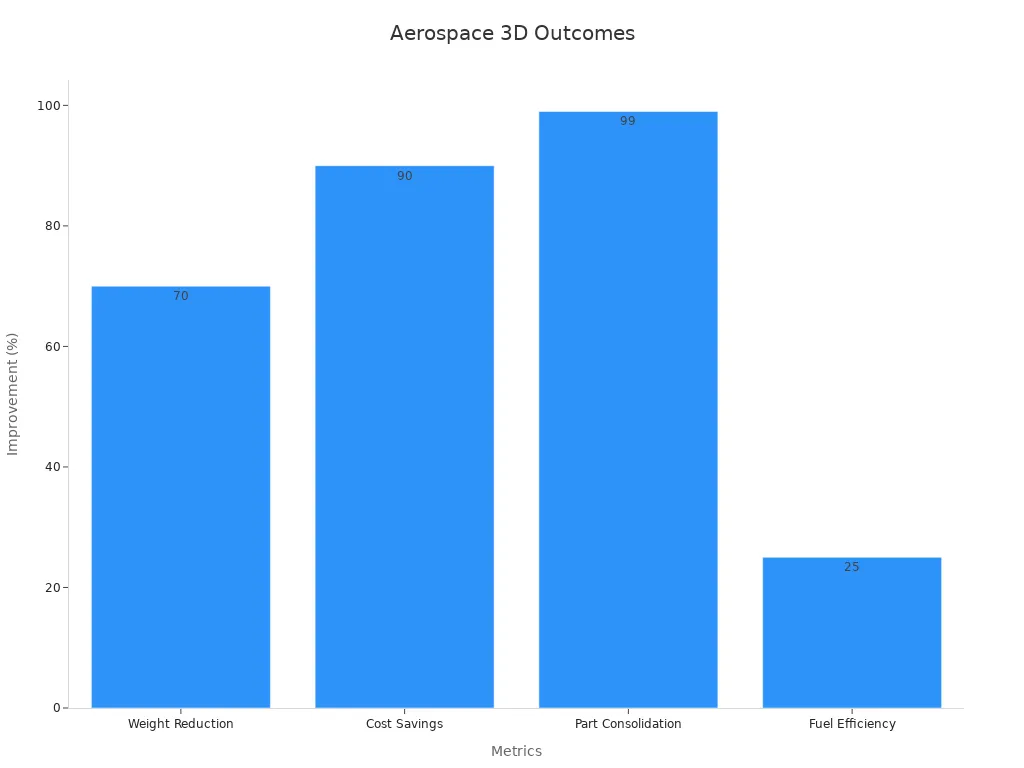
Researchers are also pushing the boundaries of design freedom. SLS enables the creation of geometries that were previously impossible, allowing you to optimize components for specific missions. Rapid prototyping accelerates innovation, while on-demand manufacturing simplifies supply chains and reduces inventory needs. Customization becomes seamless, enabling you to adapt designs for unique spacecraft requirements.
Future advancements include larger build volumes for producing bigger components, aerospace-grade materials tailored for SLS, and AI-driven designs. Machine learning is being used to create optimized parts with enhanced performance. Additionally, in-space manufacturing is gaining traction, offering the potential to produce parts during long-duration missions. This capability could revolutionize how you approach spacecraft maintenance and construction.
The integration of these technologies will redefine aerospace manufacturing. By adopting these innovations, you can expect faster production cycles, reduced costs, and more efficient spacecraft designs, ensuring a sustainable and accessible future for space exploration.
3D printing is reshaping rocket development by introducing faster production cycles, cost-efficient manufacturing, and innovative designs. You can now create lightweight rocket components that reduce fuel consumption by up to 15%, accelerating the pace of aerospace innovation. Rapid prototyping allows swift testing and iteration, ensuring rockets meet stringent performance standards.
The sustainability of 3D printing further enhances its appeal. Using titanium powders consumes 73% less energy and lowers carbon emissions by 78%. These advancements not only reduce costs but also make space exploration more accessible. As companies like Relativity Space and NASA continue to pioneer fully 3D-printed rockets, the future of aerospace manufacturing promises unprecedented efficiency and scalability.
Note: The transformative potential of 3D printing lies in its ability to redefine rocket design and production, paving the way for sustainable and affordable space exploration.
FAQ
What is the main advantage of using 3D printing in rocket development?
3D printing allows you to create rocket components faster and at a lower cost. It reduces material waste and enables the production of complex geometries that traditional methods cannot achieve. This innovation accelerates development cycles and enhances design flexibility. 🚀
How does 3D printing improve rocket performance?
3D printing enhances performance by enabling precise manufacturing of intricate designs, such as cooling channels in combustion chambers. These features optimize heat dissipation and improve engine efficiency. You can also consolidate multiple parts into one, reducing failure points and increasing reliability.
Which materials are commonly used in 3D-printed rockets?
You’ll find materials like titanium alloys, Inconel, and GRCop alloys frequently used in 3D-printed rockets. These materials offer high strength, heat resistance, and durability, making them ideal for critical components like engines and structural supports.
Can 3D printing reduce the cost of space exploration?
Yes, 3D printing significantly lowers costs by minimizing material waste and eliminating the need for expensive tooling. Studies show it can reduce production expenses by 30-40%, making space missions more affordable and accessible.
Are fully 3D-printed rockets reliable?
Fully 3D-printed rockets, like Relativity Space’s Terran 1, have demonstrated reliability through rigorous testing. By reducing part counts and using advanced materials, these rockets minimize potential failure points and enhance overall durability.
Tip: Staying informed about advancements in 3D printing can help you understand its growing role in aerospace innovation.
Lascia un commento
Tutti i commenti sono moderati prima di essere pubblicati.
Questo sito è protetto da hCaptcha e applica le Norme sulla privacy e i Termini di servizio di hCaptcha.