When you rely on supports in 3D printing, several challenges arise that can hinder efficiency and sustainability, showcasing some of the disadvantages of 3D printing. Material waste becomes a significant issue, with up to 33% of 3D prints ending up as waste. In the UK alone, filament-based 3D printing generates around 400,000 kg of plastic waste annually. Removing supports also requires extra effort, often leading to surface imperfections. These disadvantages of 3D printing highlight why understanding the pros and cons is crucial for optimizing your workflow.
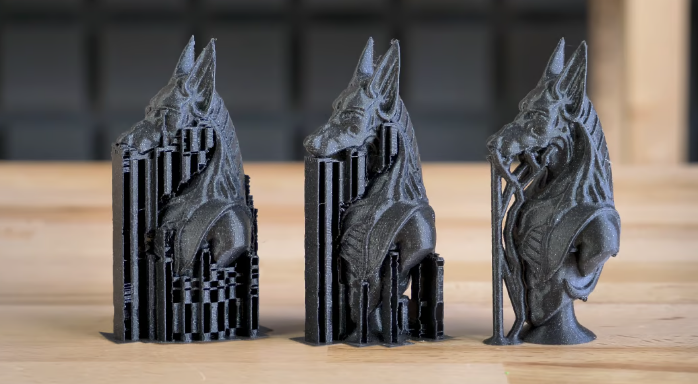
Key Takeaways
- Adding supports in 3D printing wastes a lot of material. About 33% of prints can become waste. Using fewer supports helps the environment.
- Taking off supports takes time and hard work. It can also damage the surface. Try using dissolvable supports or better designs to fix this problem.
- Making models with fewer overhangs saves money and time. Learn ways to print without supports to boost creativity.
Increased Material Usage and Waste
Material consumption due to supports
When you use supports in 3d printing, the material consumption increases significantly. Supports act as scaffolding to stabilize overhangs or complex geometries during the printing process. However, these structures are not part of the final product. They often require additional filament, which can account for 20-50% of the total material used in a single print. This extra usage directly impacts the efficiency of your 3d printing projects.
You might notice that larger or more intricate designs demand even more support material. This can lead to higher costs, especially when using premium filaments like carbon fiber or flexible materials. Additionally, the need for supports limits the potential for optimizing material usage, making it harder to achieve sustainable 3d printing practices.
Environmental impact of waste
The waste generated by supports poses a significant environmental challenge. After removing supports, you are left with non-reusable scraps that often end up in landfills. Most 3d printing filaments, such as PLA or ABS, are not biodegradable under standard conditions. This contributes to the growing problem of plastic pollution.
If you frequently rely on supports, the cumulative waste from multiple prints can become substantial. For example, hobbyists and professionals alike generate kilograms of waste annually. To mitigate this, you should explore alternative methods, such as designing models with fewer overhangs or using soluble support materials. These strategies can help reduce the environmental footprint of your 3d printing activities.
Post-Processing Challenges
Effort required for support removal
Removing supports from 3d printing models can be a time-consuming and labor-intensive process. You often need tools like pliers, cutters, or even specialized equipment to separate the supports from the printed object. This step requires precision, especially when dealing with intricate designs or fragile materials. The effort involved in support removal increases with the complexity of the model. For example, a design with numerous overhangs or tight spaces may demand more time and patience to clean up effectively.
In addition to the physical effort, you must also consider the mental focus required. A single mistake during this process can compromise the integrity of your print. This makes support removal a critical step in achieving a successful 3d printing outcome. To streamline this process, you might explore alternative methods, such as using soluble supports or adjusting your design to minimize the need for supports.
Risk of surface damage during removal
Support removal poses another challenge: the risk of damaging the surface of your 3d printing model. When you detach supports, the contact points between the supports and the model often leave marks or imperfections. These blemishes can detract from the overall quality of your print, especially if you aim for a smooth and polished finish.
You may also encounter issues like tearing or chipping, particularly with delicate materials. This risk increases if you apply excessive force or use inappropriate tools during the removal process. To mitigate these problems, you should handle the model carefully and consider post-processing techniques like sanding or polishing. These steps can help restore the surface quality, but they add to the overall time and effort required for 3d printing.
Surface Quality Issues
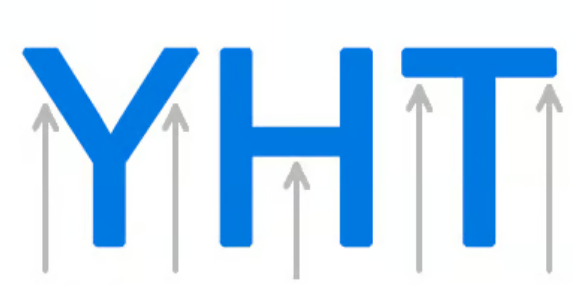
Imperfections from support contact
When you print models with supports, the areas where the supports touch the model often suffer from poor surface quality. These imperfections are especially noticeable on the underside of the part. The contact points between the supports and the model can leave visible marks, creating a messy appearance. This issue becomes more pronounced when using standard support settings, as the material tends to fuse with the initial layers of the part. Once you remove the supports, the fused material can leave pitted or uneven layers, which detract from the overall quality of your 3d printing project.
The type and spacing of supports also play a significant role in surface quality. For instance:
- Honeycomb supports often result in rougher surfaces compared to rectilinear supports.
- A 1mm rectilinear support spacing produces fewer visible marks and a cleaner finish than a 2mm spacing.
By carefully selecting support settings, you can minimize these imperfections, but achieving a flawless surface remains challenging.
Difficulty achieving smooth finishes
Achieving a smooth finish on models printed with supports requires additional effort. The marks left by support structures often demand post-processing techniques like sanding, filing, or chemical smoothing. These steps add time and labor to your 3d printing workflow. Even with meticulous post-processing, restoring the original surface quality can be difficult, especially for intricate designs or delicate materials.
You may also find that certain materials, such as PLA, are more prone to retaining imperfections after support removal. This makes it harder to achieve a polished look without compromising the model's structural integrity. To reduce the need for extensive finishing, you should consider optimizing your design to minimize supports or experimenting with soluble support materials.
Design Limitations
Reduced creative freedom
When designing models for 3d printing, you often face limitations due to the need for supports. These structures restrict your ability to create intricate or unconventional designs. Overhangs, bridges, and complex geometries may require additional supports, which can compromise the aesthetic and functional aspects of your model. You might find yourself simplifying designs to reduce the need for supports, which can stifle creativity.
For example, creating organic shapes or detailed features becomes challenging when you must account for support structures. This limitation can be particularly frustrating for artists, engineers, or hobbyists aiming to push the boundaries of 3d printing. By focusing on support-free techniques, you can regain some creative freedom. However, this often requires advanced design skills and software tools.
Designing for minimal supports
Optimizing your designs to minimize supports is essential for improving efficiency and reducing waste in 3d printing. By carefully planning your model's orientation and geometry, you can significantly lower the need for support structures. For instance, angling overhangs at 45 degrees or less can eliminate the requirement for supports in many cases.
A notable example of design optimization comes from a case study on a 3d-printed nasal osteotomy task trainer. The study focused on reducing support usage through design improvements. The findings revealed that the model could be printed with minimal deformity without supports, enhancing its accessibility and cost-effectiveness for surgical training.
Aspect |
Details |
---|---|
Case Study |
3D-printed nasal osteotomy task trainer |
Focus |
Minimizing support usage through design improvements |
Key Findings |
The model can be printed with minimal deformity without support |
Conclusion |
Design optimization enhances accessibility and cost-effectiveness |
By applying similar strategies, you can achieve better results while reducing material waste and post-processing efforts.
Cost Implications
Higher material costs
Using supports in 3d printing significantly increases material consumption, which directly impacts your costs. Every support structure requires additional filament, often amounting to 20-50% of the total material used for a single print. This extra usage becomes even more expensive when you work with premium filaments like carbon fiber or flexible materials. For instance, a project that might only require 100 grams of filament without supports could demand 150 grams or more when supports are necessary.
The financial burden doesn't stop at material costs. You also need to account for wasted filament from removed supports, which cannot be reused in most cases. This waste adds up over time, especially if you frequently print complex designs. By optimizing your models to reduce supports, you can lower material costs and improve the overall efficiency of your 3d printing workflow.
Increased labor and time expenses
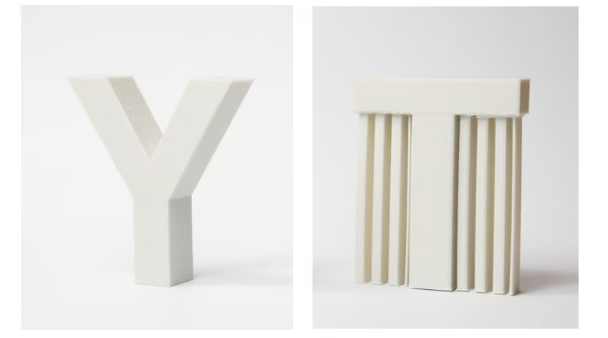
Post-processing tasks, particularly support removal, demand significant time and effort. You often need specialized tools and a steady hand to carefully detach supports without damaging the model. This process becomes even more labor-intensive for intricate designs with tight spaces or delicate features.
According to Mohsen Seifi, vice president of global advanced manufacturing programs at ASTM International, "It is commonly understood that the time and cost to perform post-processing is high. It is even higher in some cases than the actual time and cost of printing the part itself."
Support removal is often the most time-consuming aspect of post-processing. This is especially true for complex 3d printing projects where precision is critical.
- Post-processing ensures that your 3d-printed parts are both functional and visually appealing.
- However, the time spent on support removal can rival or even exceed the time it takes to print the part itself.
These additional labor and time expenses make it essential to evaluate whether supports are truly necessary for your design. Exploring alternative techniques, such as reorienting your model or using soluble supports, can help you save both time and money.
The disadvantages of 3D printing models with supports include material waste, post-processing challenges, surface imperfections, design restrictions, and increased costs. These issues often arise due to the reliance on support structures during printing.
- Many 3D printed parts require post-processing, leading to additional material waste and higher costs.
- Certain methods, like FDM, produce weaker surfaces that need refinement, further increasing expenses.
- Limited material options in 3D printing also contribute to inefficiencies and waste.
To optimize your workflow, focus on designing models with fewer overhangs, explore support-free techniques, and invest in advanced tools for support removal. Understanding the pros and cons of 3D printing helps you make informed decisions and achieve better results.
FAQ
What are the best ways to reduce support material in 3D printing?
You can reduce support material by optimizing your design. Use angles under 45 degrees, reorient your model, or explore support-free printing techniques.
How do soluble supports improve post-processing?
Soluble supports dissolve in water or specific solutions. This eliminates manual removal, reduces surface damage, and simplifies post-processing for intricate or delicate designs.
Are there specific software tools to minimize supports?
Yes, slicer software like Cura or PrusaSlicer offers advanced settings. These tools help you adjust support density, placement, and orientation for better efficiency.
Yorum bırak
Tüm yorumlar yayınlanmadan önce denetlenir.
Bu site hCaptcha ile korunuyor. Ayrıca bu site için hCaptcha Gizlilik Politikası ve Hizmet Şartları geçerlidir.